Unlocking the Potential of Plastic Mold Manufacturing
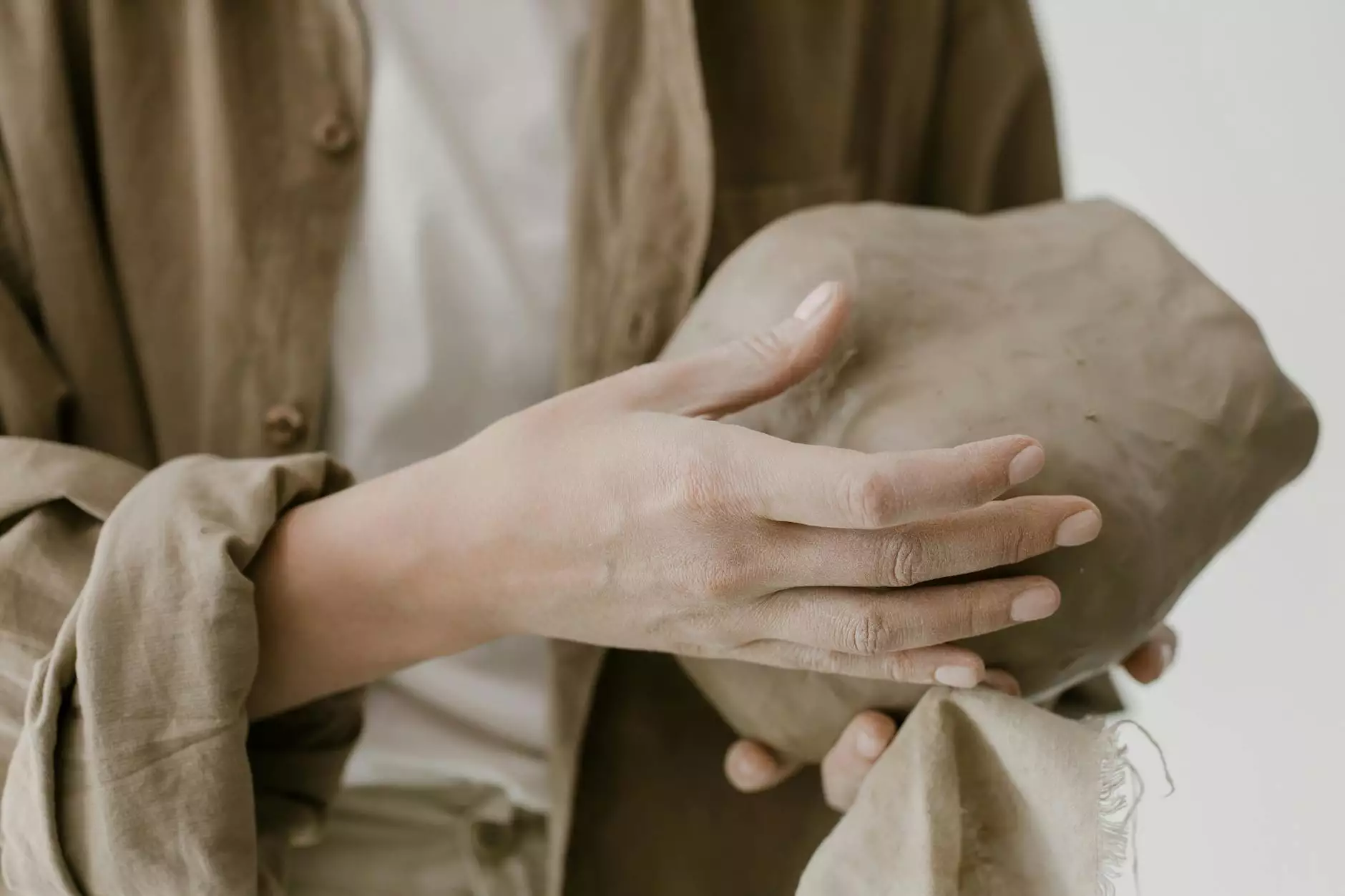
In today's dynamic market, plastic mold manufacturing stands as an essential pillar for numerous industries, significantly impacting product design and efficiency. As companies increasingly seek innovative solutions to meet customer demands, the processes and techniques utilized in plastic molding have evolved, showcasing unparalleled adaptability and precision.
Understanding the Basics of Plastic Mold Manufacturing
At its core, plastic mold manufacturing involves creating a mold that shapes liquid plastic into specific forms or objects. This method has revolutionized how products are designed and produced across various sectors, including automotive, consumer goods, medical devices, and electronics.
Key Components of the Plastic Mold Manufacturing Process
- Design and Prototyping: The journey begins with design software that assists engineers in visualizing the final product. 3D modeling simulates how the mold will perform, ensuring optimal design efficiency.
- Mold Creation: Once the design is approved, manufacturers create the mold typically from metals like steel or aluminum. This phase requires precision engineering to guarantee the finest quality output.
- Injection Molding: The actual plastic mold manufacturing process often involves injection molding, where heated liquid plastic is injected into the mold cavity.
- Cooling and Ejection: After injection, the mold cools, solidifying the plastic. The finished product is then ejected, ready for finishing processes.
- Quality Control: Rigorous quality checks ensure that the molded parts meet the required specifications, securing durability and reliability.
The Advantages of Plastic Mold Manufacturing
Plastic mold manufacturing offers a myriad of benefits, making it a favored choice in production across various industries:
1. Cost Efficiency
One of the primary advantages of plastic mold manufacturing is its cost-effectiveness. Once the mold is created, the cost per unit for mass production decreases significantly. This efficiency allows businesses to scale up production without incurring excessive costs, positioning them competitively in the market.
2. High Precision and Reproducibility
Plastic molds create consistent and accurate components with tight tolerances. This precision is vital for industries, such as automotive and aerospace, where the integrity of each part is paramount. Manufacturers can expect uniformity in every batch produced, which boosts overall quality.
3. Versatility in Design
With advancements in technology, plastic mold manufacturing has become increasingly versatile. Designers can explore complex geometries and intricate patterns that were previously difficult or impossible to create. This versatility opens the door for innovation, allowing businesses to differentiate their products in the market.
4. Lightweight and Durable Products
Plastic components manufactured through molding are not only lightweight but also exhibit remarkable durability. This characteristic is essential for applications in electronics and consumer products, where weight and sturdiness directly influence consumer experience.
5. Environmentally Friendly Options
Today, plastic mold manufacturing embraces sustainable practices with the use of recyclable materials and eco-friendly processes. Many manufacturers are now employing bioplastics, which offer similar performance without the adverse environmental impacts of traditional plastics.
Applications of Plastic Mold Manufacturing
The versatility of plastic mold manufacturing enables it to serve a wide range of applications:
1. Automotive Industry
In the automotive sector, manufacturers rely heavily on plastic molds to produce interior and exterior components. Items such as dashboards, light housings, and battery casings benefit from plastic's lightweight properties.
2. Medical Devices
Medical devices often require high precision and reliability. Products like syringes, surgical instruments, and casings for diagnostic equipment are crafted through certified plastic mold manufacturing processes, ensuring compliance with stringent health regulations.
3. Consumer Goods
From kitchenware to toys, plastic molding plays a crucial role in producing everyday items. The ability to create intricate designs at a low cost makes it ideal for consumer products, enhancing user experience through functional design.
4. Electronics
The electronic industry benefits from plastic mold manufacturing through the production of cases, connectors, and other components. The robustness, paired with aesthetic appeal, makes molded parts a desirable choice for many electronics manufacturers.
Choosing the Right Partner for Plastic Mold Manufacturing
For businesses looking to incorporate plastic mold manufacturing into their production processes, selecting the right partner is crucial. Here are key factors to consider:
- Experience and Expertise: Look for manufacturers like DeepMould, who have a proven track record in the field of plastic molding and metal fabrication.
- Technology and Equipment: Ensure they use the latest technology and equipment, which can significantly affect production efficiency and quality.
- Quality Assurance Practices: Choose a partner with robust quality control measures in place to ensure the products meet industry standards.
- Customization Capabilities: Find a supplier that offers customization services to meet specific needs and product specifications.
The Future of Plastic Mold Manufacturing
The future of plastic mold manufacturing appears bright as technology continues to evolve. Innovations such as additive manufacturing, automation, and advanced materials are set to transform the industry. These advancements will not only improve efficiency but will also enhance product capabilities, paving the way for even more applications of molded plastics.
Embracing Industry 4.0
As businesses move towards Industry 4.0, integrating IoT (Internet of Things) into plastic mold manufacturing could lead to improved manufacturing processes. Enhanced data analytics can help businesses predict maintenance needs, reducing downtime and optimizing production schedules.
Investing in Sustainability
Sustainability is more crucial than ever. The shift towards biodegradable plastics and sustainable practices in manufacturing aligns with global efforts to reduce environmental impacts. Manufacturers investing in these areas will undoubtedly gain a competitive edge in the marketplace.
Conclusion
In summary, plastic mold manufacturing is an indispensable aspect of modern production processes across multiple industries. Its advantages, including cost-effectiveness, precision, versatility, and environmental sustainability, make it a top choice for manufacturers. As technology and practices evolve, the scope of plastic mold manufacturing will only expand, offering businesses new avenues for innovation and growth. Choose wisely when selecting a manufacturing partner, and ensure that you are aligned with those at the forefront of this dynamic industry.