Understanding LEV Compliance in Newport: Ensuring a Safe Working Environment
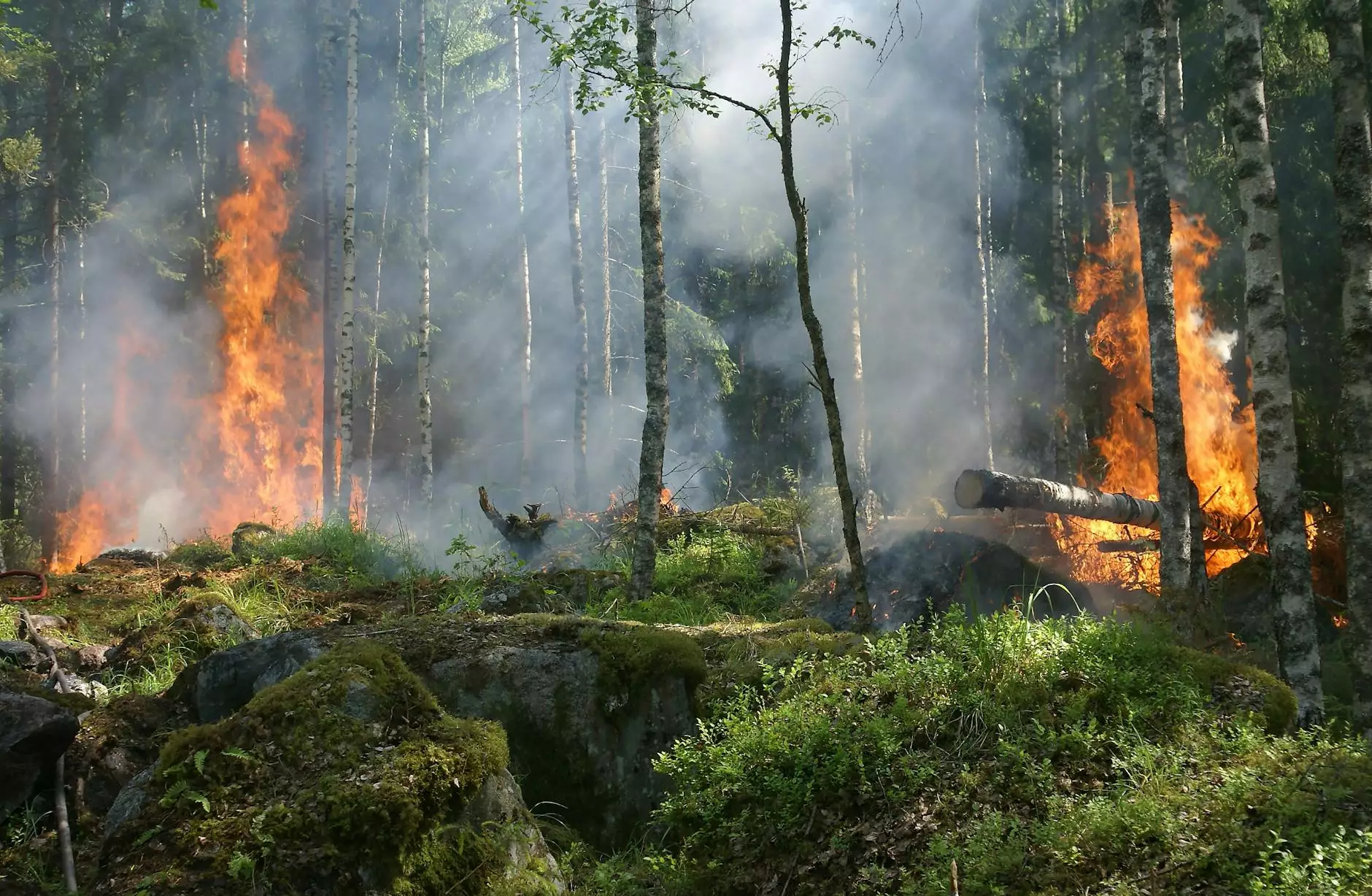
LEV (Local Exhaust Ventilation) compliance is a critical aspect of workplace safety and air quality management in Newport and beyond. For businesses in various sectors, especially those involved in Home & Garden industries, such as gardening and pest control, understanding and adhering to LEV compliance is essential. This comprehensive article will explore what LEV compliance entails, its significance for businesses, and practical tips for maintaining a safe work environment that aligns with legal standards.
What is LEV Compliance?
LEV compliance refers to the regulations and standards governing the use of local exhaust ventilation systems designed to control airborne contaminants in the workplace. These systems capture harmful dust, fumes, or vapors at the source before they can spread throughout the environment. LEV systems are particularly crucial in industries where hazardous materials are used, such as in pest control and gardening sectors, ensuring a safe and healthy environment for workers and customers alike.
The Importance of LEV Compliance
Adhering to LEV compliance is vital for multiple reasons:
- Health and Safety: Protects employees from exposure to harmful substances and reduces the risk of respiratory diseases and other health issues.
- Legal Obligations: Compliance with health and safety regulations is a legal requirement; failing to meet these standards can result in penalties and legal action.
- Business Reputation: Demonstrating commitment to worker safety enhances your business's reputation, promoting trust among clients and regulators.
- Operational Efficiency: A well-maintained LEV system can improve air quality, contributing to better overall productivity.
Understanding the LEV Compliance Process
To ensure compliance with LEV regulations, businesses need to undertake several key steps:
1. Conducting a Risk Assessment
The first step in achieving LEV compliance in Newport is conducting a thorough risk assessment. This involves identifying potential sources of airborne contaminants in the workplace, analyzing the level of risk associated with each source, and determining the appropriate control measures needed to mitigate these risks. It’s crucial to evaluate the working conditions and materials used in your operations.
2. Selecting the Appropriate LEV System
Once the risk assessment is complete, businesses should select an LEV system that effectively addresses the identified hazards. There are various types of LEV systems available, including:
- Fume Extractors: Used primarily in welding and soldering operations to filter out harmful fumes.
- Dust Collectors: Ideal for operations generating large amounts of dust, such as woodworking or construction.
- Containment Booths: Useful for isolating operations that generate volatile chemicals, particularly in the pest control industry.
3. Installation and Maintenance
After selecting the appropriate system, proper installation by qualified professionals is crucial. Regular maintenance is equally important to ensure that the LEV system operates efficiently. Business owners should establish a maintenance schedule that includes:
- Regular inspections of the ventilation system.
- Checking for filter replacement and cleaning.
- Performance testing to ensure that the system effectively captures contaminants.
4. Employee Training and Engagement
Even the best LEV systems can fail if employees are not adequately trained in their use. Businesses should invest in training programs that inform employees about the importance of LEV systems and how to use them effectively. Engaging employees in safety practices reinforces a culture of safety within the organization.
Legal Requirements for LEV Compliance
In Newport, as well as the broader UK, there are specific legal requirements that businesses must adhere to concerning LEV compliance:
- Health and Safety at Work Act 1974: This legislation places a duty on employers to ensure the health, safety, and welfare of their employees.
- Control of Substances Hazardous to Health (COSHH): Regulations require employers to control substances that can be hazardous to health, which includes implementing effective LEV systems.
- Provision and Use of Work Equipment Regulations (PUWER): These regulations mandate that equipment, including ventilation systems, is suitable for the intended use and maintained in a safe condition.
Consequences of Non-Compliance
Failure to comply with LEV regulations can result in severe consequences for businesses, including:
- Legal Action: Non-compliance can lead to prosecutions or hefty fines from regulatory bodies.
- Health Risks: Inadequate ventilation can result in serious health issues for employees, leading to increased absenteeism and reduced productivity.
- Negative Publicity: A company's reputation can suffer significantly if it is found to be non-compliant, damaging customer trust and potentially leading to loss of business.
Best Practices for Achieving LEV Compliance
To effectively manage LEV compliance, consider the following best practices:
1. Regular Audits and Inspections
Conducting regular audits of your LEV system can help ensure that it is functioning as intended. This includes checking for proper airflow, ensuring filters are not clogged, and verifying that employees are using the system correctly. Regular audits also help identify potential issues before they become significant problems.
2. Documentation and Record Keeping
Keeping thorough records of all compliance activities, including risk assessments, maintenance logs, training sessions, and audits, is crucial. This documentation can be invaluable in demonstrating compliance during inspections or audits by regulatory bodies.
3. Stay Informed About Changes in Regulations
Regulations surrounding workplace safety and LEV compliance can change. Staying informed about any updates ensures that your business remains compliant and avoids potential penalties. Engaging with professional organizations or consultancies can be a reliable source of the latest information.
4. Promote a Safety Culture
Encouraging a culture of safety within the workplace is essential for maintaining LEV compliance. Employees should feel empowered to report issues, suggest improvements, and participate in safety training sessions. A proactive approach to workplace safety benefits everyone.
Conclusion
In conclusion, focusing on LEV compliance in Newport is not merely about legal obligations; it is about creating a safe and healthy environment for employees and customers alike. By understanding the significance of LEV systems, following best practices, and staying compliant with regulations, businesses can mitigate risks and enhance their operational efficiency.
Whether you are part of the Home & Garden sector, gardening, or pest control, ensuring your workplace adheres to LEV compliance standards is essential. Not only does it protect your workforce, but it also reflects your commitment to responsible and ethical business practices.
lev compliance newport