The Incredible Impact of CNC Lathed Parts in Modern Manufacturing
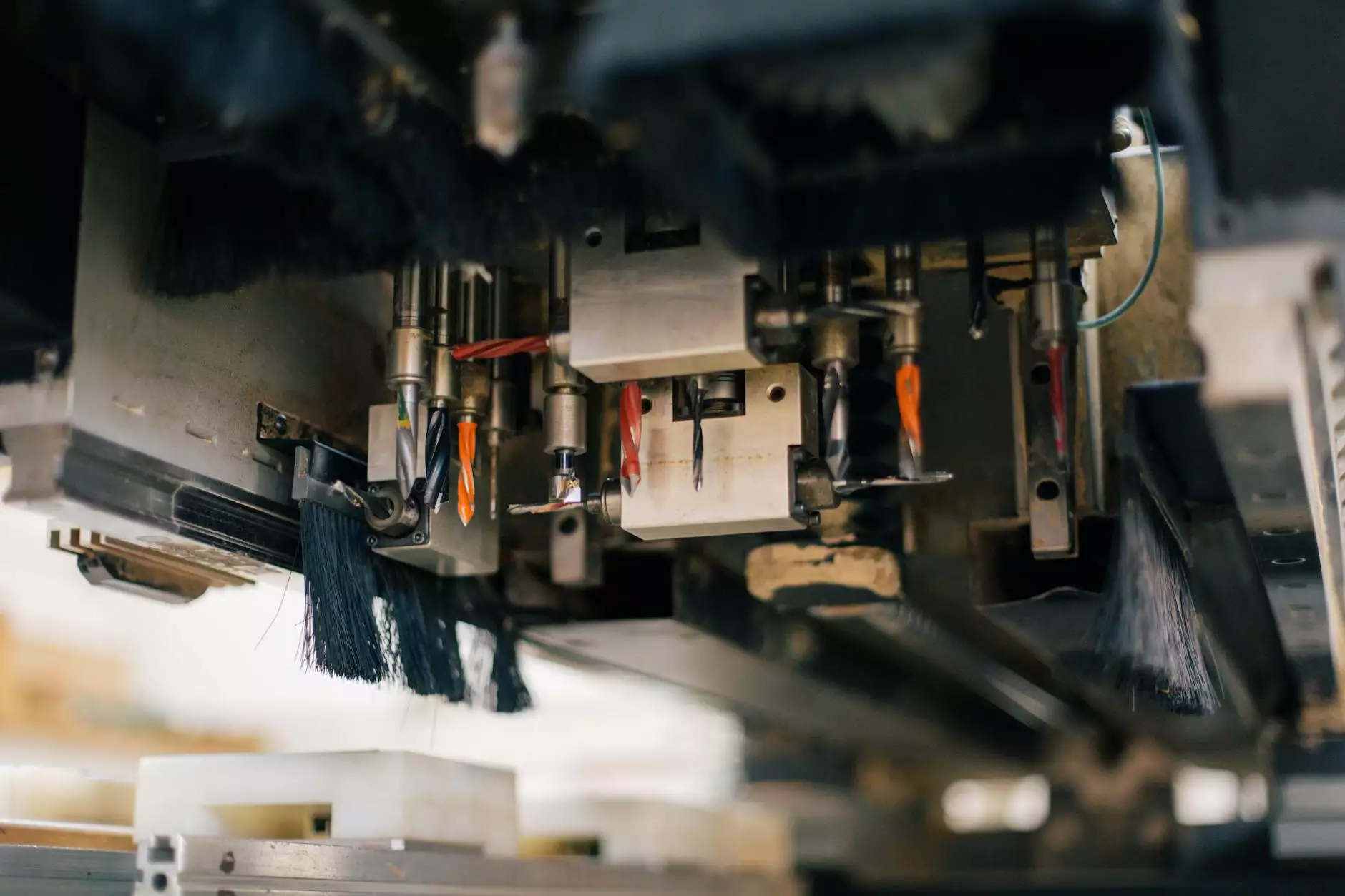
In today's fast-paced industrial landscape, CNC lathed parts have emerged as a pivotal element driving the efficiency and precision of metal fabrication. With the surge in demand for high-quality components across various sectors, understanding the capabilities and advantages of CNC lathing can significantly benefit businesses in their pursuit of excellence.
Understanding CNC Lathing: A Technical Overview
CNC lathing is a sophisticated process that utilizes computer numerical control (CNC) technology to manipulate a lathe for machining materials with remarkable precision. This method automates the cutting process, allowing for consistent replication of complex designs that meet stringent tolerances. The system operates on a series of programmed instructions, which dictate the movements of the cutting tools.
Key Components of CNC Lathing
- Lathe Machine: The core machinery that rotates the workpiece against cutting tools.
- CNC Controller: The computer interface that executes the programmed design and controls machine operations.
- Tooling: A variety of cutting tools utilized for different machining tasks, tailored to specific materials and desired outcomes.
- Workpiece: The raw material or pre-formed component that undergoes the lathing process.
Benefits of Using CNC Lathed Parts
CNC lathed parts offer a myriad of benefits that make them an optimal choice for various applications in industries such as automotive, aerospace, and electronics.
1. Enhanced Precision and Accuracy
One of the primary advantages of CNC lathing is its exceptional precision. CNC technology allows for extremely fine tolerances, which is essential in applications where even the slightest deviation can lead to failures. This high level of accuracy ensures that components fit perfectly in their intended assemblies.
2. Increased Production Efficiency
CNC machines can operate continuously without the need for breaks, leading to significantly increased production rates. This efficiency not only accelerates manufacturing but also reduces labor costs, allowing companies to allocate resources more effectively.
3. Versatility in Production
CNC lathes can be programmed to produce a wide variety of geometrically complex parts. From simple cylindrical shapes to intricate designs requiring various machining techniques, the versatility of CNC lathed parts makes them suitable for many different industries.
4. Consistency and Repeatability
Once programmed, CNC machines can replicate the same part with consistent quality over and over again. This reliability is crucial for businesses that rely on uniform components to maintain quality standards in their products.
5. Capability for Complex Designs
With advanced software and programming capabilities, CNC lathes can create complex geometric shapes that would be impossible or highly labor-intensive to produce manually. This aspect allows engineers and designers to innovate without worrying about the feasibility of production.
Applications of CNC Lathed Parts
The applications of CNC lathed parts are as diverse as the industries utilizing them. Here are some notable uses:
- Automotive Industry: Precision components such as gears, shafts, and brackets are critical in automotive manufacturing, where performance and safety are paramount.
- Aerospace Sector: The aerospace industry demands high-strength, lightweight parts that can withstand extreme conditions. CNC lathing provides the necessary quality and performance characteristics.
- Electronics: Components like connectors, housings, and mounting brackets require intricate details and finely tuned specifications, making CNC lathing a preferred method.
- Medical Devices: From surgical instruments to implantable devices, the high precision of CNC lathed parts is essential for functionality and safety in medical applications.
Choosing the Right Metal Fabricators
When selecting a partner for CNC lathed parts production, it is crucial to choose a reputable metal fabricator who understands the intricacies of CNC machining. Here are key factors to consider:
1. Experience and Expertise
A company with extensive experience in CNC lathing will have the knowledge to handle complex designs and materials. Look for metal fabricators who have successfully completed projects similar to your needs.
2. Equipment and Technology
Modern facilities equipped with the latest CNC technology are essential for high-quality output. Ensure that the fabricator maintains up-to-date machines that can produce intricate CNC lathed parts efficiently.
3. Quality Control Measures
Robust quality control processes must be in place to ensure that every part produced meets the required specifications. Inquire about the fabricator’s quality assurance testing methods.
4. Customization Capabilities
The ability to customize parts according to specific requirements is vital. A versatile metal fabricator should offer tailored solutions that meet industry standards and client specifications.
Future Trends in CNC Lathed Parts
The landscape of metal fabrication is continuously evolving. Several emerging trends in CNC lathing promise to shape the future of CNC lathed parts:
1. Automation and Smart Manufacturing
The integration of IoT and smart technology into production processes is leading to increased automation. This shift not only enhances efficiency but also enables real-time monitoring of production, further minimizing errors.
2. Advanced Materials
As industries seek stronger yet lighter materials, CNC lathes will evolve to work with advanced composites and alloys that provide better performance while maintaining manufacturability.
3. Sustainable Practices
Environmental concerns are influencing manufacturing processes. Sustainable practices such as waste reduction and recycling will become integral in the production of CNC lathed parts, pushing companies toward greener initiatives.
4. Software Innovations
Improvements in CAD/CAM software will enhance design capabilities, allowing for even more intricate designs to be programmed and machined with ease.
Conclusion: Embracing the Future of CNC Lathed Parts
In summary, CNC lathed parts are at the forefront of the metal fabrication revolution, providing manufacturers with tools to create precise, efficient, and versatile components. As technology advances and industries demand higher standards, the role of CNC lathing will only become more critical. By partnering with experienced metal fabricators like deepmould.net, businesses can leverage the benefits of CNC machining to stay competitive in the ever-evolving market.